SignTorch
Artist
We can re-use the motors, wire harness, limit switches, and gantry.
All we need for stage 1 is:
Power supply
Breakout board
Two servo drives
One stepper driver
One limit switch (optional)
Two buttons
One connector (optional)
Each part is detailed separately.
And some software
Mach3 - to control the machine and process g-code (required to start)
Sheetcam - to convert from vectors to gcode with lead-ins, kerf compensation, etc. (not required to start)
As for wire, you'll need some 2 and 4 conductor stranded cable with shield and drain. 20 awg is good for signals. Motor power wires can be 16 awg. It is best to use fully shielded wiring everywhere on CNC to guard against potential noise issues.
Adding basic and advanced height control will involve additional parts and minor wire reconfiguration.
It's best to plan and provide for electronic enclosures, and mount all controls in their enclosure before starting wiring.
I wired mine out on the bench and will have to rewire most of the controls to fit them in an enclosure. Don't do that.
You'll have to plan your own enclosures, but I'd have one for the motor drivers and BOB on the machine, and one for the power supply on the floor.
I moved the wire harness hanger and exit point from the near left to the far right which gets it out of the way and makes the front of the machine more open.
Here's what it looks like, the controls are on the right behind the monitor. I used plastic wire loom to run my stepper motor cable along the harness cable to the carriage.
I modified the rails so it comes apart easier and is easier to move around.
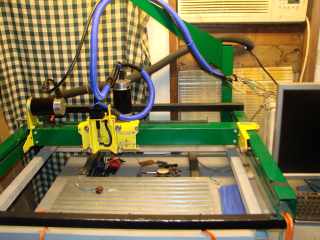
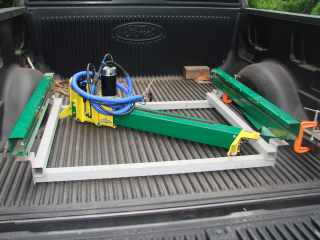
All we need for stage 1 is:
Power supply
Breakout board
Two servo drives
One stepper driver
One limit switch (optional)
Two buttons
One connector (optional)
Each part is detailed separately.
And some software
Mach3 - to control the machine and process g-code (required to start)
Sheetcam - to convert from vectors to gcode with lead-ins, kerf compensation, etc. (not required to start)
As for wire, you'll need some 2 and 4 conductor stranded cable with shield and drain. 20 awg is good for signals. Motor power wires can be 16 awg. It is best to use fully shielded wiring everywhere on CNC to guard against potential noise issues.
Adding basic and advanced height control will involve additional parts and minor wire reconfiguration.
It's best to plan and provide for electronic enclosures, and mount all controls in their enclosure before starting wiring.
I wired mine out on the bench and will have to rewire most of the controls to fit them in an enclosure. Don't do that.
You'll have to plan your own enclosures, but I'd have one for the motor drivers and BOB on the machine, and one for the power supply on the floor.
I moved the wire harness hanger and exit point from the near left to the far right which gets it out of the way and makes the front of the machine more open.
Here's what it looks like, the controls are on the right behind the monitor. I used plastic wire loom to run my stepper motor cable along the harness cable to the carriage.
I modified the rails so it comes apart easier and is easier to move around.
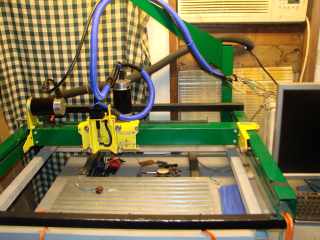
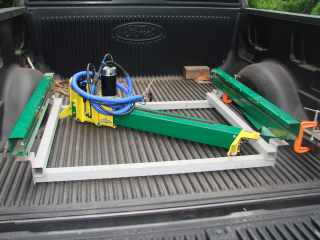